2016 Wood Diamond Award Best Of/Best Overall: Woodperfect Custom Cabinetry
Dollar Amount: Over $50,000
Briefly describe your business and the type of products manufactured.
Woodperfect Custom Cabinetry (Forney, TX) is a second generation, family owned and operated custom cabinetry manufacturer. Their featured product line is European style cabinetry, however, they also are well versed in American face frame product, providing all their products in a variety of materials and finishes. They are full service, and their clientele ranges from Commercial General Contractors and the Residential Building Industry to the Architecture and Design communities, as well as individual homeowners. They possess a staff trained in vast areas of expertise, along with having both professionally trained engineering and design professionals, enabling them to provide services customarily outside the scope of many of their competitors.
What materials/species were used in this project/item?
Apalachian Red Oak
Columbia Forest Products – PureBond plywood
Fire rated 2 x 4’s
Powder Coated CNC Cut Aluminum
3Form 2” Chroma White Out
Uba Tuba Granite
Sea Pearl Quartzite
ML Campbell Finishing Products
Led Lighting
Hafele hinges
Grass DynaPro 3D
Describe, in detail, the project/item's construction
The project was a complete overhaul and refresh of a Copeland’s Restaurant and Bar where the original existing single-sided bar was opened and replicated on the opposing side to double bar patron capacity along with complete dining room refresh on an intensive and unforgivingly short time line. Finished bar size was approximately 45’L x 30’W. Project also encompassed the utilization and replication of much of the existing crown, base and trim as feasible.
The planning stages of the project took over a year to not only strive for, but achieve what has been considered an impossible feat in the industry and involved owners, managers, general contractors, cities, bar, kitchen and maintenance personnel, designers, architects and engineers, subcontractors and vendors, just to name a few. Ultimately, the timing was determined and the final plan was unveiled in early July. The restaurant and bar would continue operations in a portion of the lobby and public areas while the actual facility would be completely closed off while undergoing construction. The timeline was not for the faint of heart – demolition kick off on August 4 and the reconstruction of the “new and improved” facility would be complete for service of customers on September 2 - no delays, no excuses, no extensions and no fluff in the schedule. Due to the adjoining facility being a hotel, construction within the facility could only commence between 7 am and 7 pm, seven days a week. Construction trades “working on top of each other” would be an understatement with crews of 35 to 50, at times, working simultaneously and harmoniously was an achievement in itself.
For us, the project immediately began in late July when funds were released to expedite the 3Form product. Given that standard lead times of 6-10 weeks for delivery of sheet goods, 12-15 weeks with fabrication and 3-4 months with LED lighting installations was definitely not in our timeline, we determined the product would be ordered as sheet goods with local fabrication. Due to the weight of the product (~500-600 lbs per 4’ x 8’ sheet), outsourcing fabrication soon became our best (while most concerning) option. We used the balance of our “pre-site” time to fabricate and finish bar surround material, fluted column material, oversized crown and base moulding, center liquor island, back bar cabinetry, etc. (all to an exacting match of existing in profile and finish); work with the metal fabricator to insure the center island decorative “Fleur De Lis” was cut to exacting standards; devising and welding a metal support system within the island cabinet to support the combined weight of a full sheet of 3Form, double-sided decorative aluminum detail, and quartzite countertop, along with bulk liquor storage; practicing perfect welding of 3Form joints so light transmission would be seemless; and experimenting with LED lighting and placement to properly light the product for desired impact.
On-site work began with surveying and reinforcing the remaining bare-bones structure of the existing bar and replicating a reverse duplicate on the now opposing side of the “new” bar. Once in place, layout of fixtures, placement of substrate materials and templates were produced for 3Form fabrication. Hearts stopped when the late afternoon call came from the 3Form fabricator on the evening the fabrication process was to begin (a special crew was commandeered for after-hours fabrication) noting the product was thicker in the center than the perimeter. Following inspection and further research with the manufacturer, we learned that the sheets are manufactured through a “pouring” process with no further milling, so they are “square” (within 1/8” tolerance) and “evenly” thick (+1/4” to -3/8” tolerance). Given that our deadline was fast approaching when product arrived, with only 1-1/2 weeks left for completion, our only choice was to proceed with fabrication having the material squared, cut to size, and correct any deficits during the installation process.
The owner elected to retain what has been a feature item in the bar, a ChillRite Frost Rail system, from the original bar installation which ran the length of the bar. However, mid installation after all components were sized and partially installed, it was determined upon installation the unit was not functioning properly, could not be repaired, and required replacement. No problem one might say (without breaking a sweat), we’ll just leave a hole for the new one – if they only manufactured them currently to the same size specifications as the original rail that EVERYTHING was planned around. Ultimately, ChillRite agreed to expedite a replacement to the original size specifications.
The balance of our time was spent finishing the back bars, strategically placing columns for suspended glass liquor shelving, dry fitting countertop materials, painstakingly welding and installing the 3Form counters along with days of non-stop tedious sanding, installation and testing of LED lighting, installation of center feature island, decorative metal and 3Form elements, granite counters, suspended glass liquor shelving and decorative glassware display racks…and more sanding, of course!
What is the most unusual aspect or outstanding characteristic of this entry?
Everything!! Transforming a dark, single-sided bar and dated dining rooms into a fresh, open and inviting environment for patrons and hotel guests is not an unusual occurrence within the hospitality industry. However, refreshing and completely transforming a Copeland’s Restaurant and Bar operating 18 hours daily, 7 days a week, 52 weeks a year within a busy Hilton Hotel in an upscale suburb near DFW airport without interruption to either guests or services is quite an undertaking by any standards…but not necessarily impossible!
The design itself is innovative and exciting, executed impeccably, and breathed new life and ambiance into an outdated restaurant and bar facility by creating a focal point easily viewed from many perspectives within the establishment, the hotel entry courtyard and beyond upon arrival.
The LED lighting of the center feature island and surrounding bar tops now ingeniously allows the bar to celebrate with their clientele in a unique way and is utilized as a drawing card to the facility during such events as football season (which is big in the local area) by lighting each side of the bar with local team colors and hosting after game happy hours. And, of course, holidays are always a time for celebration at Copeland’s with red and green lights during the Christmas season, green lights for St. Patrick’s Day, etc. and lest we not forget the roots of Copeland’s which is always celebrated with the familiar purple, green and yellow lights of Mardi Gras! We knew instantly this would be a great attraction while working at night experimenting with the lights on the bar tops and patrons would knock on the windows when they couldn’t find entry and ask what it was and when it would be open…can’t get much better than that in the hospitality industry.
Adding to the focal point of the center feature island, not only was the countertop material changed to Sea Pearl Quartzite which actually glows itself under the lighting, but the 6” reverse bevel knife edge was extremely difficult to process and unique in it’s own right.
The frost rail provides patrons not only with ice cold beer, but a unique and inviting experience being meticulously imbedded in an already unique bar top.
But, from our perspective, the most unusual aspect has to be that despite the magnitude of the project and lack of time, it was a project that was enjoyable, went virtually as flawless as any project (though we had concerns more than once along the way) and with a substantial portion of the project resting on our shoulders, we made it to completion with time to spare and the clients were ecstatic over the final results!
How has being a member of the CMA benefited you and/or your business?
I would, without a doubt, say the single, most important benefit I derive from being a member of the CMA is that of having a network of professionals, like me, knowledgable and experienced in virtually any area I may encounter. The eagerness to share hard earned expertise and assist fellow cabinet makers among the membership through forums and/or personal contact has proven itself invaluable time and time again. I have personally realized the savings of time, money, resources, failure and sometimes I have been provided the wisdom to “just simply say no” when I might not have otherwise reached that conclusion on my own. Everyone becomes a mentor in their own unique role – honestly, what business could not benefit from that type of relationship?
The second real benefit I derive is credibility. Being a member of a national and well respected organization provides me with a competitive edge, alleviating the “fly by night” persona sometimes associated with this industry. The marketing benefits including additional presence, both online and in print, along with the Wood Diamond Awards, have enabled me to capitalized upon my successes, and work to not only enhance, but forward my own individual marketing efforts by setting me apart from other shops in my area. I expect those benefits will only increase as the efforts of the organization increases.
List any items that were outsourced.
3Form
3Form Fabrication
Fleur Di Lies and Glassware Metal Fabrication and Powder Coating
¾” Tempered Glass
Granite and Quartzite Fabrication and Installation
LED lighting
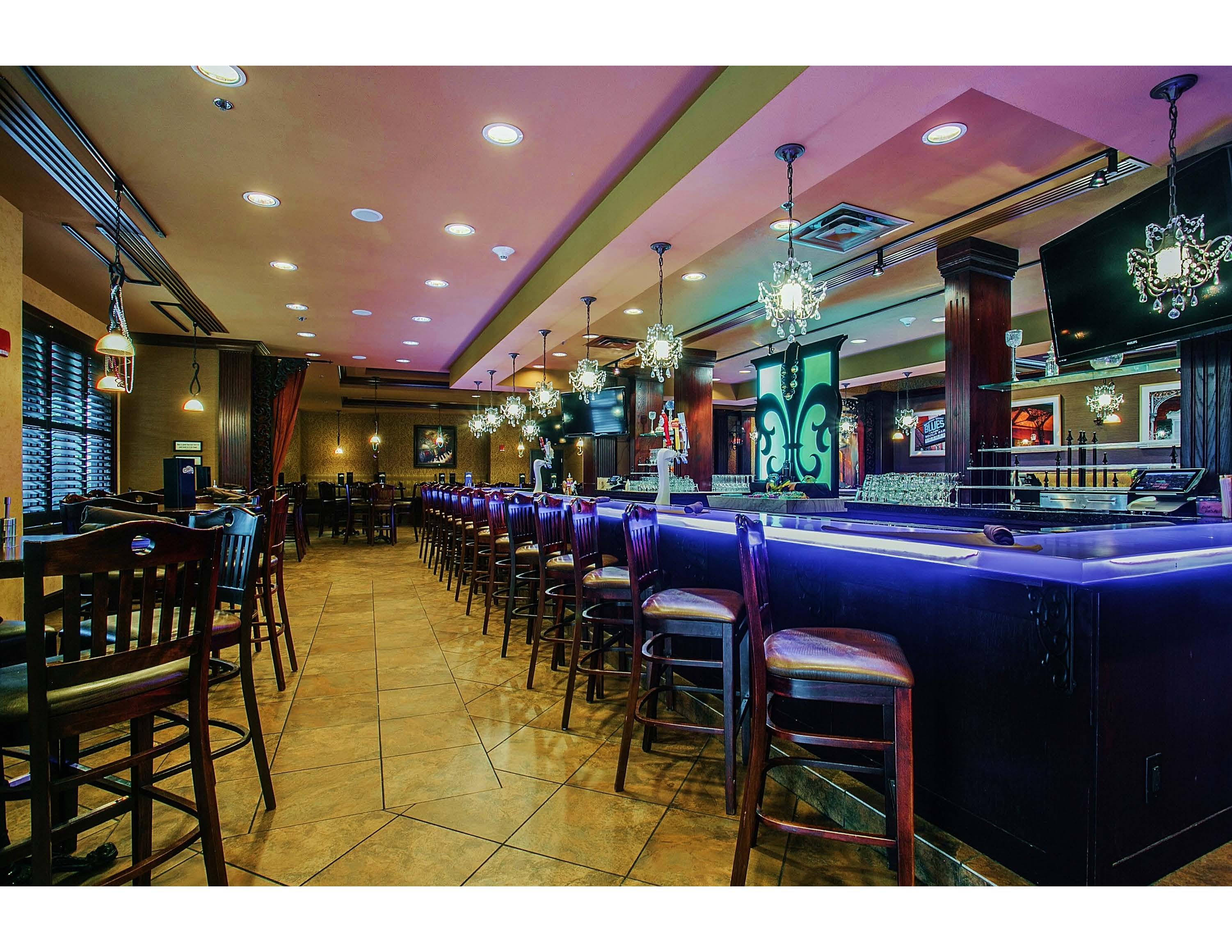